Intro
Explore 3D printable engine models, featuring intricate designs, precise engineering, and customizable parts, ideal for makers, engineers, and hobbyists seeking realistic prototypes and scale models.
The world of 3D printing has revolutionized the way we create and design objects, and one of the most exciting applications of this technology is in the creation of 3D printable engine models. For car enthusiasts, engineers, and hobbyists, 3D printable engine models offer a unique opportunity to explore the inner workings of complex machines in a highly detailed and interactive way. In this article, we will delve into the world of 3D printable engine models, exploring their benefits, working mechanisms, and the steps involved in creating these incredible models.
The importance of 3D printable engine models cannot be overstated. For educational purposes, these models provide a hands-on way for students to learn about the intricacies of engine design and function. By being able to see and interact with each component, learners can gain a deeper understanding of how engines work, which can be invaluable for those pursuing careers in engineering or mechanics. Moreover, for professionals, 3D printable engine models can serve as valuable tools for demonstrating concepts, testing designs, and communicating ideas with precision.
The complexity and detail of 3D printable engine models are truly astounding. From the minutest details of piston heads to the overall architecture of the engine block, every aspect can be meticulously designed and printed. This level of detail allows for the creation of models that are not only visually stunning but also highly educational. Whether it's a scale model of a vintage car engine or a modern, high-performance motorcycle engine, the possibilities are endless, and the accuracy of the models can be astounding.
Benefits of 3D Printable Engine Models
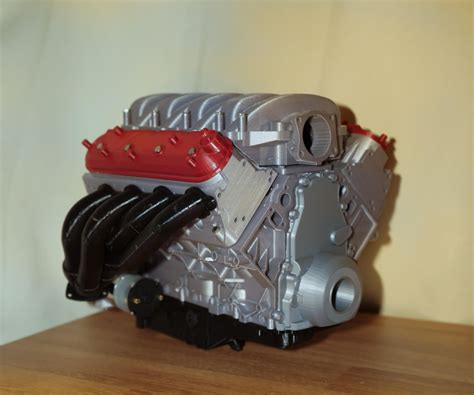
One of the primary benefits of 3D printable engine models is their educational value. By providing a tangible, three-dimensional representation of engine components and their relationships, these models can significantly enhance the learning experience. They allow students and enthusiasts to explore the engine's design and operation in a way that is both engaging and informative. Additionally, 3D printable engine models can be customized to highlight specific aspects of engine design or to demonstrate particular concepts, making them highly versatile educational tools.
Another significant advantage of 3D printable engine models is their potential for cost savings. Traditional methods of creating detailed engine models can be extremely costly, involving extensive machining, casting, or other manufacturing processes. In contrast, 3D printing offers a relatively inexpensive way to produce highly detailed models, especially when considering the cost per unit in small production runs. This makes 3D printable engine models accessible to a wider range of individuals and organizations, from hobbyists to educational institutions.
Customization and Detailing
The level of customization and detailing possible with 3D printable engine models is one of their most appealing aspects. Designers can create models that reflect any desired level of complexity, from simplified representations of engine components for educational purposes to highly detailed, accurate models of specific engines for enthusiasts or professionals. This customization extends to the materials used for printing as well, allowing for a range of textures, colors, and properties that can enhance the realism and durability of the models.Working Mechanisms of 3D Printable Engine Models
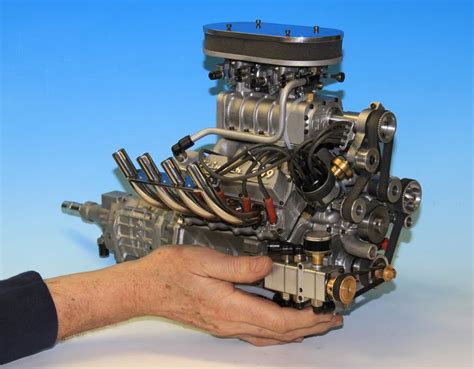
Understanding the working mechanisms of 3D printable engine models involves grasping both the design principles behind their creation and the physical processes that govern their operation. In terms of design, these models are typically created using computer-aided design (CAD) software, which allows designers to draft detailed, precise models of engine components and assemblies. The CAD files are then used to guide the 3D printing process, layer by layer constructing the model according to the designer's specifications.
The physical operation of 3D printable engine models can range from static displays that showcase engine design to functional models that demonstrate the motion of engine components. For functional models, the working mechanisms are designed to mimic the real-world operation of an engine as closely as possible, given the limitations of the materials and scale. This can include moving parts such as pistons, crankshafts, and camshafts, which are carefully designed and printed to ensure smooth operation and accuracy.
Design and Printing Process
The design and printing process for 3D printable engine models is intricate and involves several key steps. First, designers use CAD software to create a digital model of the engine or its components. This stage requires a deep understanding of engine design, 3D modeling techniques, and the capabilities and limitations of 3D printing technology. Once the design is complete, it is sliced into layers and sent to a 3D printer, which constructs the model layer by layer using the chosen printing material.The choice of printing material is crucial, as it affects the model's durability, appearance, and functionality. Common materials include plastics such as ABS and PLA, which offer a good balance between cost, ease of printing, and model properties. For more specialized applications, other materials like metal-filled filaments or resin may be used to achieve specific textures or properties.
Steps Involved in Creating 3D Printable Engine Models
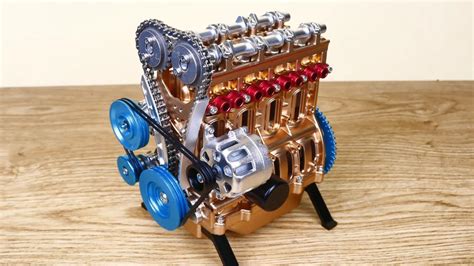
Creating 3D printable engine models involves several steps, from initial design conception through to the final printed product. The first step is research and planning, where designers gather reference materials and decide on the scope and level of detail for the model. This is followed by the design phase, where the model is created using CAD software. Designers must ensure that the model is not only accurate and detailed but also optimized for 3D printing, taking into account factors such as material usage, print time, and potential supports needed during printing.
Once the design is finalized, the next step is preparing the model for printing. This includes slicing the model into layers and configuring the printing settings to achieve the desired quality and properties. The actual printing process can take several hours or even days, depending on the model's complexity and the printer's capabilities. After printing, the model may require post-processing, such as removing supports, sanding, or applying a finish, to enhance its appearance and durability.
Post-Processing and Finishing
Post-processing and finishing are critical steps in creating 3D printable engine models, as they can significantly affect the model's appearance and overall quality. Common post-processing techniques include removing supports or raft material left over from the printing process, sanding to smooth out layer lines or rough edges, and applying paints or coatings to enhance the model's realism and durability.For models intended to be highly detailed or to mimic the appearance of real engine components, additional finishing techniques may be employed. These can include applying metal plating or powder coating to give the model a metallic appearance, using decals or stickers to add detailed labels or logos, or even integrating electronic components to create illuminated or moving parts.
Practical Examples and Applications
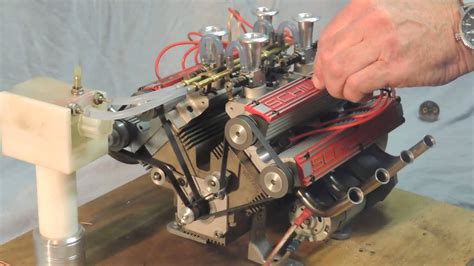
3D printable engine models have a wide range of practical applications across various fields. In education, they can be used as teaching tools to help students understand complex engine concepts in a more engaging and interactive way. For professionals, these models can serve as prototypes for testing and validating engine designs, reducing the need for costly and time-consuming traditional prototyping methods.
Enthusiasts and hobbyists also benefit from 3D printable engine models, as they can create highly detailed and accurate models of their favorite engines for display or to learn more about their operation. Furthermore, the customization potential of 3D printing allows for the creation of models that reflect specific engine modifications or upgrades, making them invaluable for those looking to understand or demonstrate the effects of such changes.
Future Developments and Trends
The future of 3D printable engine models looks promising, with ongoing advancements in 3D printing technology and materials science expected to further enhance the capabilities and applications of these models. One trend is the increasing use of advanced materials, such as carbon fiber-reinforced polymers or metallic alloys, which can provide models with enhanced strength, durability, and realism.Another area of development is the integration of functional components into 3D printed engine models, allowing for the creation of models that not only demonstrate engine operation but can also perform tasks such as generating power or propulsion. This could lead to new applications in fields like robotics, aerospace, and automotive engineering, where functional prototypes and models are crucial for innovation and development.
3D Printable Engine Models Gallery
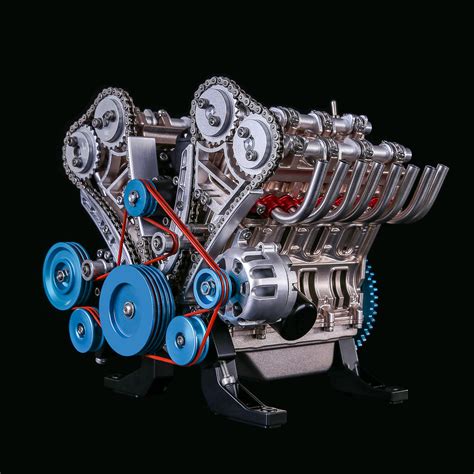
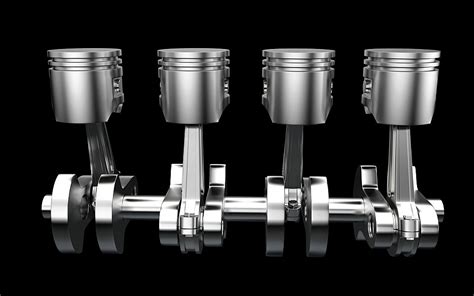
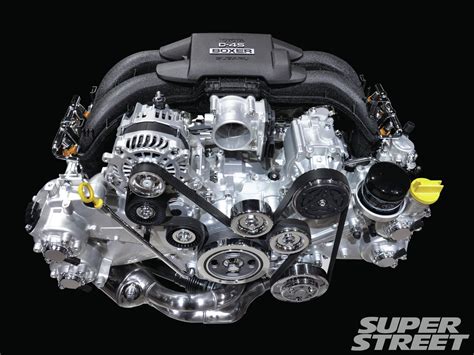
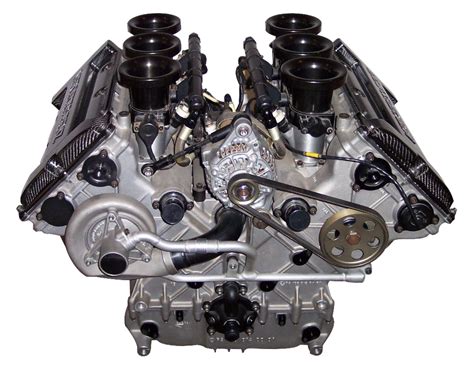
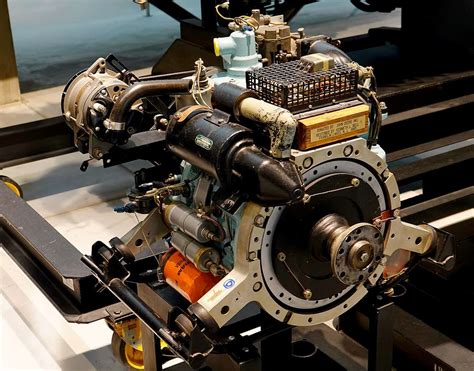
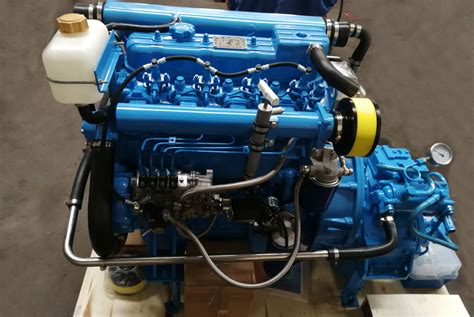

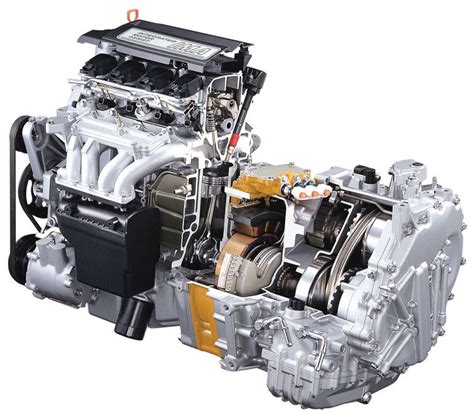
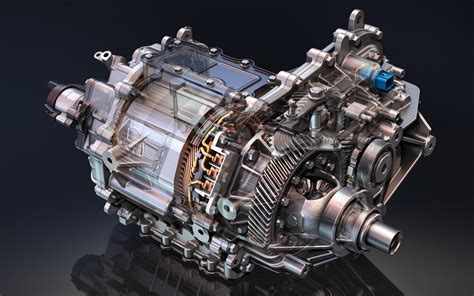
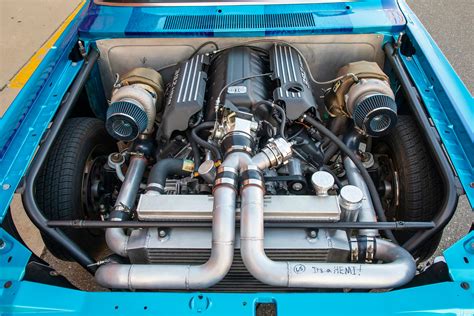
What are the benefits of 3D printable engine models for educational purposes?
+3D printable engine models offer a hands-on, interactive way for students to learn about engine design and operation, enhancing their understanding and engagement with complex concepts.
How do 3D printable engine models contribute to cost savings in prototype development?
+By allowing for the rapid creation of detailed, accurate models at a lower cost than traditional manufacturing methods, 3D printable engine models can significantly reduce the expenses associated with prototype development and testing.
What role do 3D printable engine models play in demonstrating engine modifications or upgrades?
+3D printable engine models can be customized to reflect specific engine modifications or upgrades, providing a visual and interactive way to demonstrate their effects and benefits, which can be invaluable for enthusiasts, professionals, and educators alike.
As we conclude our exploration of 3D printable engine models, it's clear that these models have the potential to revolutionize the way we learn about, design, and interact with engines. Whether you're an educator looking for innovative teaching tools, a professional seeking to prototype and test engine designs, or an enthusiast eager to explore the intricacies of your favorite engines, 3D printable engine models offer a unique combination of detail, accuracy, and interactivity. We invite you to share your thoughts, experiences, and projects related to 3D printable engine models in the comments below and to explore the possibilities that this exciting technology has to offer.