Intro
Discover expert 3D printable zip tie tips, including design optimization, printing techniques, and material selection for strong and durable zip ties, perfect for DIY projects and makers.
The world of 3D printing has opened up a wide range of possibilities for creating innovative and functional objects. One such object that has gained popularity among makers and DIY enthusiasts is the 3D printable zip tie. Zip ties, also known as cable ties, are used to manage cables and wires, keeping them organized and tidy. With the ability to 3D print custom zip ties, users can create tailored solutions for their specific needs. In this article, we will delve into the world of 3D printable zip ties, exploring their benefits, working mechanisms, and providing tips for printing and using them.
The importance of cable management cannot be overstated. A well-organized cable setup not only improves the aesthetic appeal of a workspace or entertainment area but also reduces the risk of damage to cables and equipment. Traditional zip ties are widely available, but they often come in standard sizes and materials, which may not be suitable for every application. This is where 3D printable zip ties come into play, offering a customizable solution that can be tailored to specific requirements. Whether you need zip ties for securing cables in a home office, organizing wires behind a TV, or managing cords in a professional setting, 3D printing technology allows you to create the perfect tool for the job.
The process of creating 3D printable zip ties involves designing the tie's shape and structure using computer-aided design (CAD) software or online tools. Once the design is finalized, it can be printed using a 3D printer. The choice of material is crucial, as it determines the durability, flexibility, and overall performance of the zip tie. Common materials used for 3D printing zip ties include PLA (polylactic acid), ABS (acrylonitrile butadiene styrene), and PETG (polyethylene terephthalate glycol), each offering its unique characteristics. For example, PLA is a popular choice due to its ease of printing and biodegradable nature, while ABS is known for its strength and impact resistance.
Benefits of 3D Printable Zip Ties
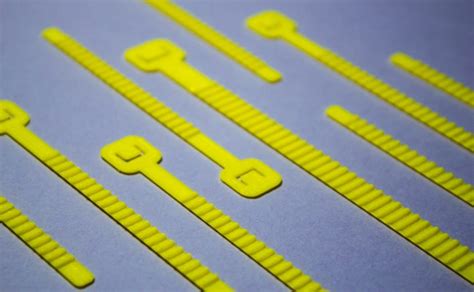
The benefits of 3D printable zip ties are numerous. Firstly, they offer customization options that are not available with traditional zip ties. Users can design zip ties with specific dimensions, shapes, and features that cater to their unique needs. This level of customization is particularly useful in applications where standard zip ties may not fit or function as required. Additionally, 3D printable zip ties can be made from a variety of materials, allowing users to choose the properties that best suit their application. For instance, if a zip tie needs to be flexible, a material like TPU (thermoplastic polyurethane) can be used, while applications requiring high strength might opt for ABS or PETG.
Another significant advantage of 3D printable zip ties is their potential for cost-effectiveness. While the initial investment in a 3D printer may seem prohibitive, the long-term savings can be substantial. Traditional zip ties are often purchased in bulk, and the cost can add up, especially for specialized or custom ties. With 3D printing, users can produce zip ties as needed, reducing waste and saving money in the process. Furthermore, the ability to print zip ties in-house can significantly reduce lead times, as users are not dependent on suppliers or manufacturers for delivery.
Working Mechanisms of 3D Printable Zip Ties
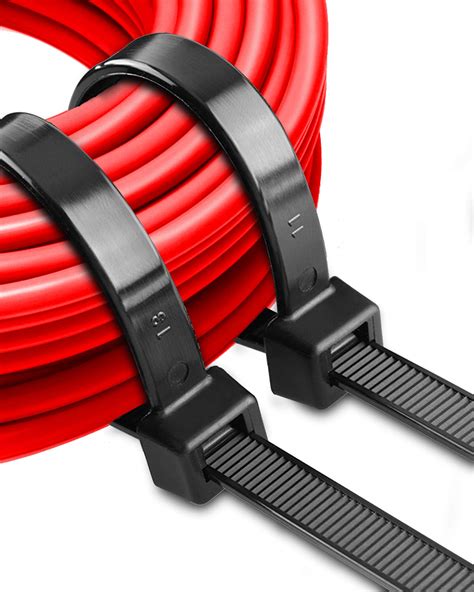
Understanding the working mechanisms of 3D printable zip ties is essential for designing and printing effective ties. The basic mechanism of a zip tie involves a toothed strap that is inserted through a spring-loaded head. As the strap is pulled through the head, it engages with the teeth, securing the cable or object in place. The design of the toothed strap and the spring-loaded head can be modified in 3D printed zip ties to enhance their performance. For example, the teeth can be designed for better grip, or the spring can be adjusted for easier or tighter closure.
The material properties also play a crucial role in the working mechanism of 3D printable zip ties. The flexibility of the material can affect how easily the tie can be wrapped around objects, while the strength of the material determines how securely it can hold cables in place. The choice of material and design should be based on the specific application of the zip tie, ensuring that it provides the necessary functionality without compromising on durability or ease of use.
Steps for Printing 3D Printable Zip Ties
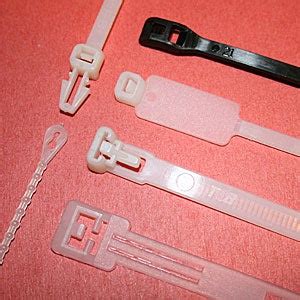
Printing 3D printable zip ties involves several steps, from designing the tie to post-printing processing. The first step is to design the zip tie using CAD software or an online design tool. This involves creating a digital model of the tie, including its shape, size, and any custom features. Once the design is complete, it is exported as an STL file, which is then imported into slicing software. The slicing software prepares the design for printing by generating G-code, which instructs the 3D printer on how to print the tie.
The next step is to select the appropriate printing settings. This includes choosing the material, layer height, infill density, and print speed. The choice of settings depends on the desired properties of the zip tie, such as strength, flexibility, and surface finish. After the printing settings are configured, the zip tie is printed. Depending on the complexity of the design and the printing settings, this can take anywhere from a few minutes to several hours.
Practical Examples and Statistical Data
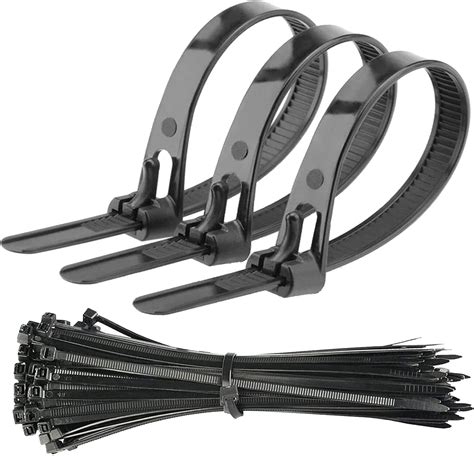
There are numerous practical examples of how 3D printable zip ties can be used in various applications. For instance, in the aerospace industry, custom zip ties can be designed to secure cables in aircraft, where space and weight are critical factors. In the automotive sector, 3D printed zip ties can be used to manage wires and cables in vehicles, providing a neat and organized appearance. In homes and offices, 3D printable zip ties can be used to organize cables and wires, reducing clutter and improving safety.
Statistical data highlights the growing demand for 3D printing technology, including the production of custom zip ties. According to industry reports, the global 3D printing market is expected to continue its rapid growth, driven by advancements in technology and the increasing adoption of 3D printing in various industries. This growth is expected to lead to more innovative applications of 3D printing, including the development of new materials and designs for zip ties.
Tips for Using 3D Printable Zip Ties
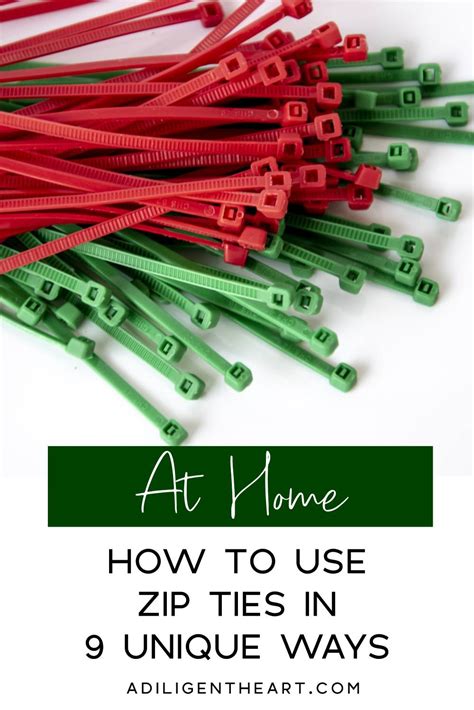
When using 3D printable zip ties, there are several tips to keep in mind. Firstly, it's essential to choose the right material for the application. Different materials offer different properties, such as flexibility, strength, and chemical resistance. Selecting the appropriate material ensures that the zip tie performs as expected and lasts for a long time. Secondly, the design of the zip tie should be carefully considered. The shape, size, and features of the tie should be tailored to the specific application, taking into account factors such as the size of the cables, the environment, and any regulatory requirements.
Another tip is to ensure proper printing settings. The quality of the print can significantly affect the performance of the zip tie. Factors such as layer height, infill density, and print speed should be optimized for the specific material and design. Additionally, post-printing processing, such as removing support material and applying a finish, can enhance the appearance and functionality of the zip tie. Finally, it's crucial to test the zip ties before using them in critical applications. This involves checking their strength, durability, and performance under various conditions to ensure they meet the required standards.
Gallery of 3D Printable Zip Ties
3D Printable Zip Ties Image Gallery
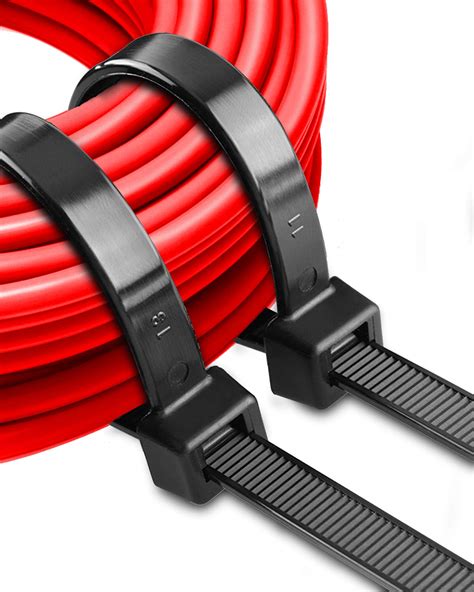
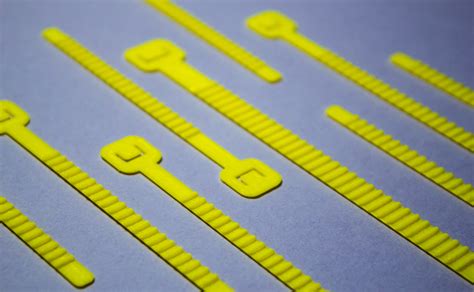
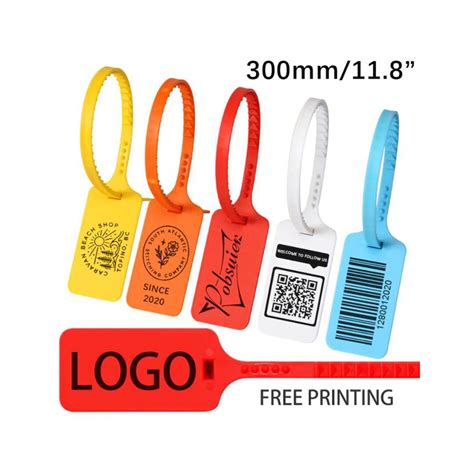
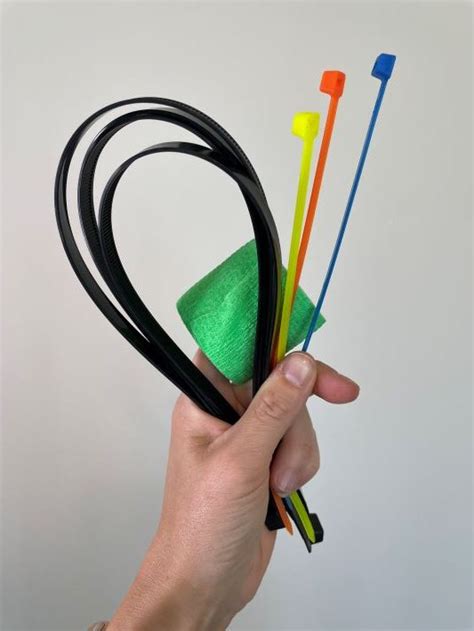
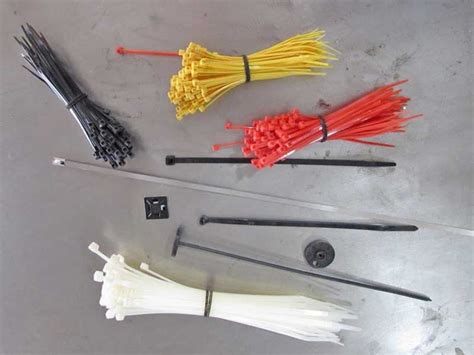
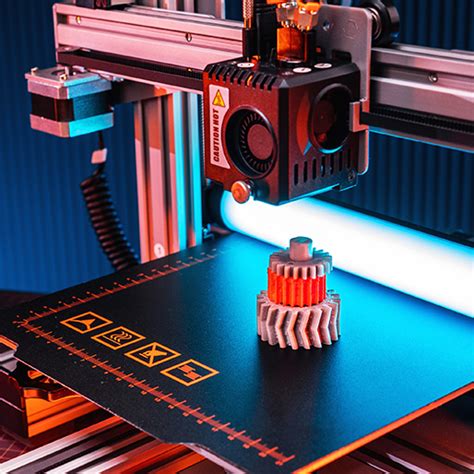
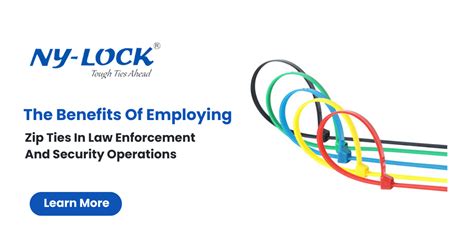
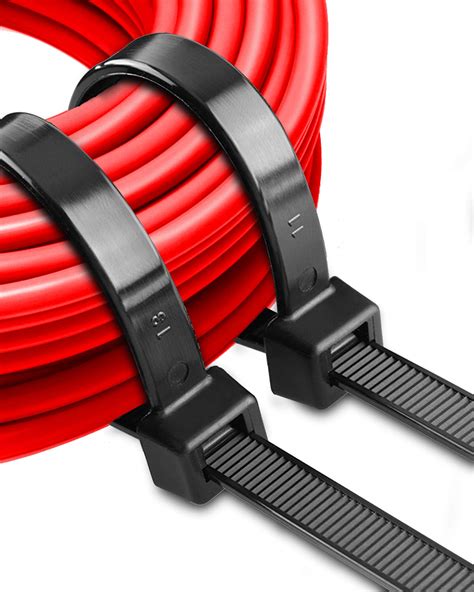
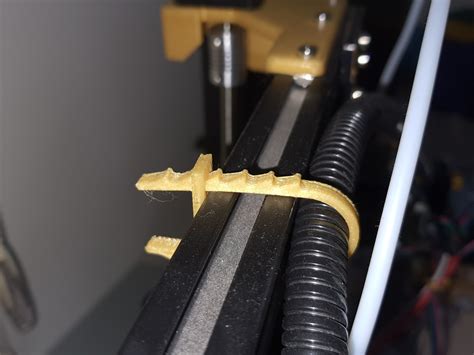
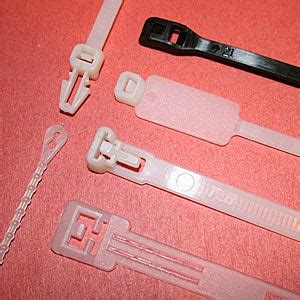
What are the benefits of using 3D printable zip ties?
+The benefits of using 3D printable zip ties include customization, cost-effectiveness, and the ability to produce ties with specific properties tailored to their application.
How do I design a 3D printable zip tie?
+To design a 3D printable zip tie, you can use CAD software or online design tools. The design should consider factors such as the shape, size, and features of the tie, as well as the material properties.
What materials can be used for 3D printing zip ties?
+Common materials used for 3D printing zip ties include PLA, ABS, PETG, and TPU. The choice of material depends on the desired properties of the zip tie, such as flexibility, strength, and chemical resistance.
How do I ensure the quality of my 3D printed zip ties?
+To ensure the quality of your 3D printed zip ties, it's essential to optimize your printing settings, use high-quality materials, and perform post-printing processing such as removing support material and applying a finish.
Can I use 3D printable zip ties in industrial applications?
+Yes, 3D printable zip ties can be used in industrial applications, provided they are designed and printed to meet the necessary standards and regulations. This may involve using specific materials, designing the tie for high strength and durability, and ensuring compliance with industry standards.
In conclusion, 3D printable zip ties offer a versatile and innovative solution for cable management, providing users with the ability to create customized ties tailored to their specific needs. With the benefits of customization, cost-effectiveness, and the potential for producing ties with unique properties, 3D printable zip ties are set to revolutionize the way we manage cables and wires. Whether you're a DIY enthusiast, a professional, or an industry expert, exploring the world of 3D printable zip ties can open up new possibilities for improving efficiency, reducing costs, and enhancing the overall quality of your work. We invite you to share your experiences, ask questions, and explore the endless possibilities that 3D printable zip ties have to offer.