Intro
Compare Lifo vs Fifo inventory methods, understanding Last-In-First-Out and First-In-First-Out techniques, inventory valuation, and cost flow assumptions to optimize stock management and financial reporting.
The way businesses manage their inventory can significantly impact their bottom line. Two of the most commonly used inventory methods are Last-In, First-Out (LIFO) and First-In, First-Out (FIFO). Understanding the differences between these two methods is crucial for businesses to make informed decisions about their inventory management. In this article, we will delve into the world of inventory management, exploring the benefits and drawbacks of LIFO and FIFO methods, and providing practical examples to help businesses choose the best approach for their needs.
The importance of inventory management cannot be overstated. It affects not only the financial performance of a business but also its ability to meet customer demand, manage storage space, and maintain a competitive edge in the market. With the rise of e-commerce and globalization, businesses are facing increasing pressure to optimize their inventory management systems. In this context, the choice between LIFO and FIFO inventory methods becomes critical. By understanding the pros and cons of each method, businesses can make informed decisions that align with their goals and objectives.
In recent years, the inventory management landscape has undergone significant changes. Advances in technology have enabled businesses to track their inventory in real-time, automate inventory management tasks, and analyze data to make better decisions. However, despite these advances, many businesses still struggle to manage their inventory effectively. This is where the LIFO and FIFO inventory methods come in. By choosing the right method, businesses can streamline their inventory management processes, reduce costs, and improve their overall performance.
Introduction to LIFO and FIFO Inventory Methods
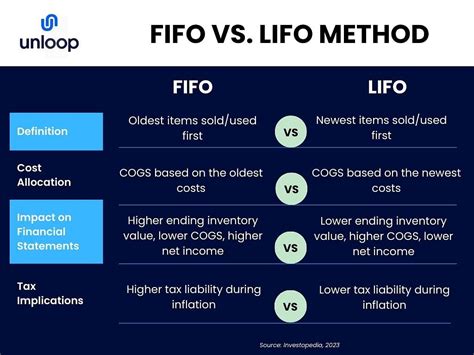
The LIFO and FIFO inventory methods are two different approaches to managing inventory. The main difference between the two methods lies in the order in which inventory items are sold or used. Under the LIFO method, the most recently acquired inventory items are sold or used first, while under the FIFO method, the oldest inventory items are sold or used first. This difference in approach can have significant implications for businesses, affecting their financial performance, tax liabilities, and ability to meet customer demand.
How LIFO Inventory Method Works
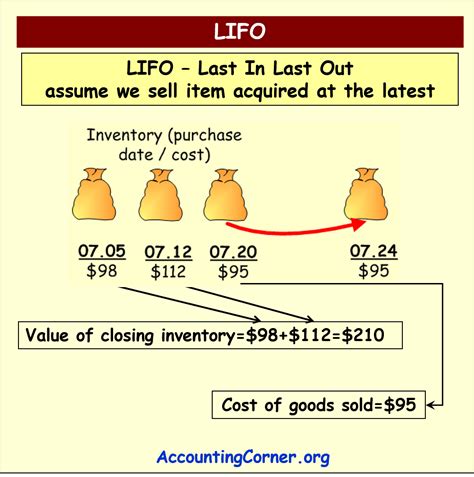
The LIFO inventory method assumes that the most recently acquired inventory items are sold or used first. This means that the oldest inventory items remain in stock, and their costs are not recognized as expenses until they are sold or used. The LIFO method is commonly used in industries where inventory items are prone to obsolescence or have a limited shelf life. For example, a fashion retailer may use the LIFO method to manage its inventory of clothing, as newer styles and designs are more likely to be sold first.
The LIFO method has several benefits, including:
- Reduced tax liabilities: By assuming that the most recently acquired inventory items are sold or used first, businesses can reduce their tax liabilities, as the costs of these items are not recognized as expenses until they are sold or used.
- Improved matching of costs and revenues: The LIFO method helps businesses match the costs of inventory items with the revenues generated from their sale, providing a more accurate picture of financial performance.
- Better management of inventory obsolescence: The LIFO method encourages businesses to manage their inventory levels carefully, as older inventory items may become obsolete or lose their value over time.
However, the LIFO method also has some drawbacks, including:
- Complexity: The LIFO method can be complex to implement and maintain, especially for businesses with large and diverse inventory holdings.
- Inaccurate valuation: The LIFO method can result in inaccurate valuation of inventory items, as the costs of older items may not reflect their current market value.
- Limited applicability: The LIFO method may not be suitable for businesses with stable or increasing inventory levels, as it assumes that inventory items are sold or used in the reverse order of their acquisition.
How FIFO Inventory Method Works
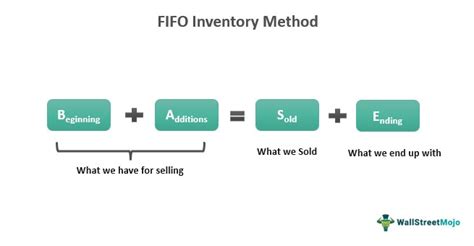
The FIFO inventory method assumes that the oldest inventory items are sold or used first. This means that the costs of these items are recognized as expenses immediately, and their values are matched with the revenues generated from their sale. The FIFO method is commonly used in industries where inventory items have a long shelf life or are not prone to obsolescence. For example, a manufacturer may use the FIFO method to manage its inventory of raw materials, as these items are not likely to become obsolete or lose their value over time.
The FIFO method has several benefits, including:
- Simple to implement: The FIFO method is relatively simple to implement and maintain, especially for businesses with small and homogeneous inventory holdings.
- Accurate valuation: The FIFO method provides an accurate valuation of inventory items, as the costs of older items are recognized as expenses immediately.
- Wide applicability: The FIFO method is suitable for businesses with stable or increasing inventory levels, as it assumes that inventory items are sold or used in the order of their acquisition.
However, the FIFO method also has some drawbacks, including:
- Increased tax liabilities: By assuming that the oldest inventory items are sold or used first, businesses may recognize higher costs as expenses, resulting in increased tax liabilities.
- Poor matching of costs and revenues: The FIFO method may not provide an accurate matching of costs and revenues, as the costs of older inventory items may not reflect their current market value.
- Inadequate management of inventory obsolescence: The FIFO method may not encourage businesses to manage their inventory levels carefully, as older inventory items may remain in stock for extended periods.
Comparison of LIFO and FIFO Inventory Methods
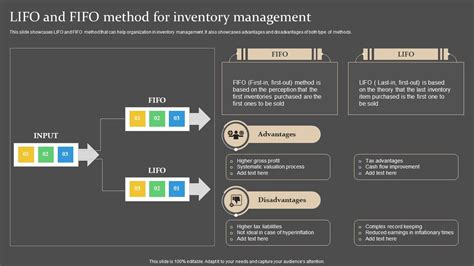
The LIFO and FIFO inventory methods have different assumptions and implications for businesses. The choice between the two methods depends on various factors, including the type of inventory items, the industry, and the business goals. Here are some key differences between the LIFO and FIFO methods:
- Assumptions: The LIFO method assumes that the most recently acquired inventory items are sold or used first, while the FIFO method assumes that the oldest inventory items are sold or used first.
- Valuation: The LIFO method can result in inaccurate valuation of inventory items, as the costs of older items may not reflect their current market value. The FIFO method provides an accurate valuation of inventory items, as the costs of older items are recognized as expenses immediately.
- Tax implications: The LIFO method can reduce tax liabilities, as the costs of the most recently acquired inventory items are not recognized as expenses until they are sold or used. The FIFO method may increase tax liabilities, as the costs of older inventory items are recognized as expenses immediately.
- Applicability: The LIFO method is suitable for businesses with inventory items that are prone to obsolescence or have a limited shelf life. The FIFO method is suitable for businesses with stable or increasing inventory levels.
Practical Examples of LIFO and FIFO Inventory Methods
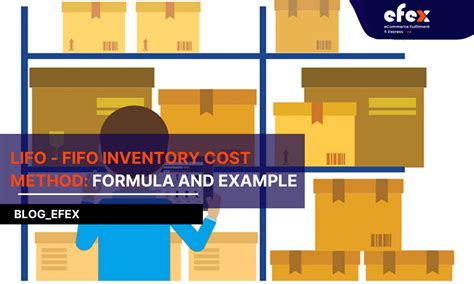
To illustrate the differences between the LIFO and FIFO inventory methods, let's consider a few practical examples:
- Example 1: A fashion retailer purchases 100 units of clothing at $10 each in January and 100 units at $15 each in June. If the retailer sells 100 units in July, the LIFO method would recognize the costs of the June purchase ($15 each) as expenses, while the FIFO method would recognize the costs of the January purchase ($10 each) as expenses.
- Example 2: A manufacturer purchases 1000 units of raw materials at $5 each in January and 1000 units at $10 each in June. If the manufacturer uses 1000 units in July, the LIFO method would recognize the costs of the June purchase ($10 each) as expenses, while the FIFO method would recognize the costs of the January purchase ($5 each) as expenses.
These examples demonstrate how the LIFO and FIFO inventory methods can result in different financial outcomes for businesses. By choosing the right method, businesses can optimize their inventory management processes, reduce costs, and improve their overall performance.
Benefits and Drawbacks of LIFO and FIFO Inventory Methods
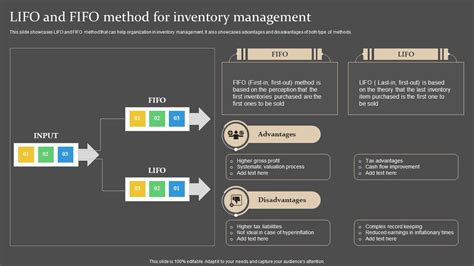
The LIFO and FIFO inventory methods have different benefits and drawbacks. Here are some of the key advantages and disadvantages of each method:
LIFO Method:
Benefits:
- Reduced tax liabilities
- Improved matching of costs and revenues
- Better management of inventory obsolescence
Drawbacks:
- Complexity
- Inaccurate valuation
- Limited applicability
FIFO Method:
Benefits:
- Simple to implement
- Accurate valuation
- Wide applicability
Drawbacks:
- Increased tax liabilities
- Poor matching of costs and revenues
- Inadequate management of inventory obsolescence
By understanding the benefits and drawbacks of each method, businesses can make informed decisions about their inventory management processes.
Choosing the Right Inventory Method
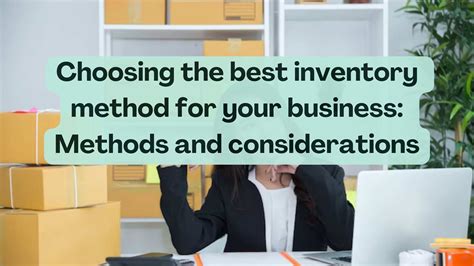
The choice between the LIFO and FIFO inventory methods depends on various factors, including the type of inventory items, the industry, and the business goals. Here are some factors to consider when choosing the right inventory method:
- Type of inventory items: If inventory items are prone to obsolescence or have a limited shelf life, the LIFO method may be more suitable. If inventory items have a long shelf life or are not prone to obsolescence, the FIFO method may be more suitable.
- Industry: The LIFO method is commonly used in industries where inventory items are prone to obsolescence, such as fashion or technology. The FIFO method is commonly used in industries where inventory items have a long shelf life, such as manufacturing or distribution.
- Business goals: If the business goal is to reduce tax liabilities, the LIFO method may be more suitable. If the business goal is to provide an accurate valuation of inventory items, the FIFO method may be more suitable.
By considering these factors, businesses can choose the right inventory method that aligns with their goals and objectives.
Gallery of Inventory Management
Inventory Management Image Gallery
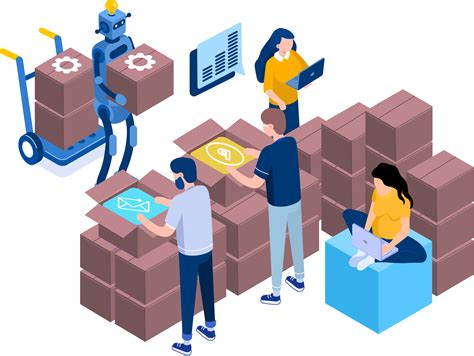
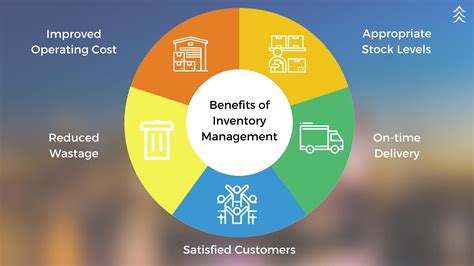
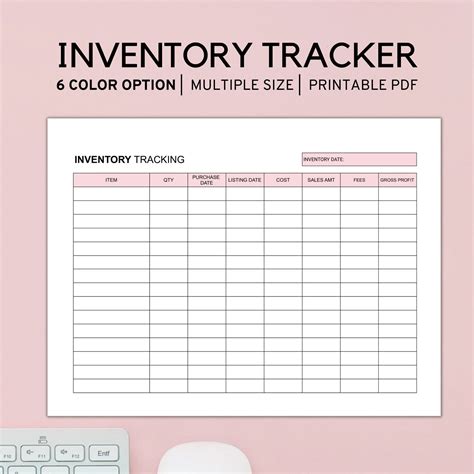
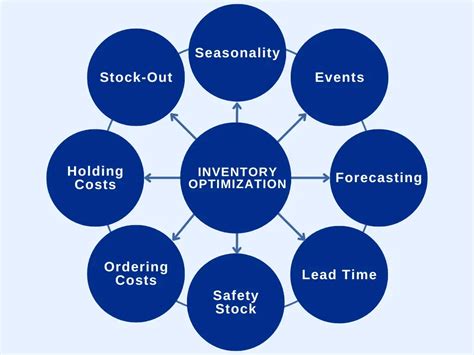
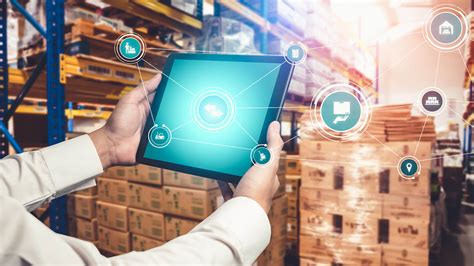
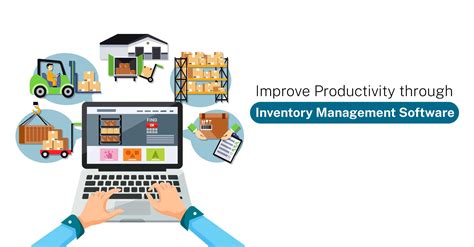
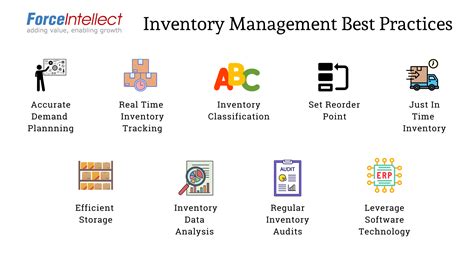
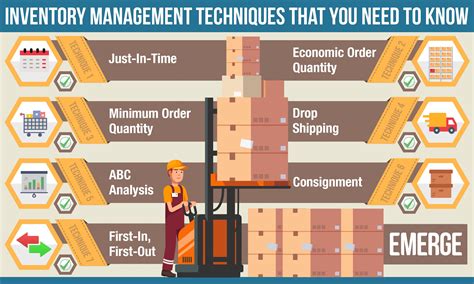
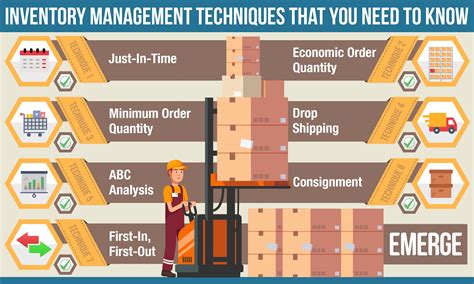
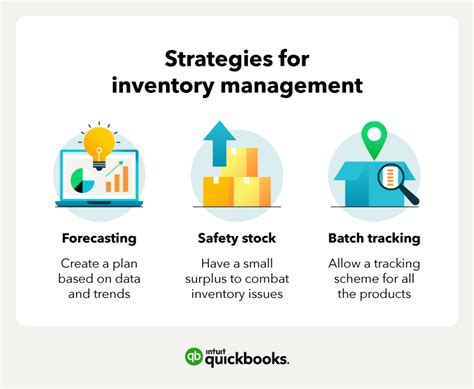
What is the main difference between LIFO and FIFO inventory methods?
+The main difference between LIFO and FIFO inventory methods is the order in which inventory items are sold or used. LIFO assumes that the most recently acquired inventory items are sold or used first, while FIFO assumes that the oldest inventory items are sold or used first.
Which inventory method is more suitable for businesses with inventory items that are prone to obsolescence?
+The LIFO inventory method is more suitable for businesses with inventory items that are prone to obsolescence, as it assumes that the most recently acquired inventory items are sold or used first.
Which inventory method provides an accurate valuation of inventory items?
+The FIFO inventory method provides an accurate valuation of inventory items, as the costs of older items are recognized as expenses immediately.
In