Intro
Discover 5 O-Ring size tips for precise sealing, including material selection, durometer, and tolerance considerations, to ensure optimal performance in various applications, such as hydraulic systems and mechanical engineering.
The importance of selecting the correct O-ring size cannot be overstated, as it plays a crucial role in ensuring the proper sealing and functioning of various mechanical systems. O-rings are used in a wide range of applications, from industrial machinery to automotive and aerospace systems. The correct O-ring size is essential to prevent leaks, maintain system pressure, and reduce the risk of equipment failure. In this article, we will delve into the world of O-rings, exploring the key factors to consider when selecting the correct size, and providing valuable tips to help you make informed decisions.
When it comes to O-ring sizing, there are several factors to consider, including the type of material, the operating temperature, and the system pressure. The correct O-ring size will depend on the specific application, and selecting the wrong size can lead to premature wear, reduced system performance, and even catastrophic failure. With so many different O-ring sizes and materials available, it can be challenging to determine the correct size for your specific application. However, by following a few simple tips and guidelines, you can ensure that you select the correct O-ring size for your needs.
The consequences of selecting the wrong O-ring size can be severe, resulting in costly repairs, downtime, and even safety risks. In contrast, selecting the correct O-ring size can help to ensure reliable system performance, reduce maintenance costs, and improve overall efficiency. Whether you are working with hydraulic systems, pneumatic systems, or other types of mechanical equipment, selecting the correct O-ring size is essential to achieving optimal performance and minimizing the risk of failure. With this in mind, let's take a closer look at some valuable tips for selecting the correct O-ring size.
O-Ring Size Selection Basics
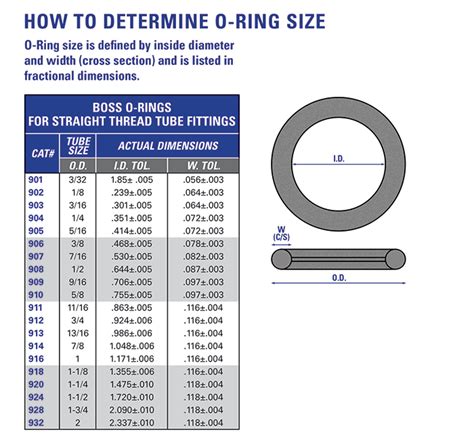
Understanding O-Ring Sizes
O-ring sizes are typically measured in inches or millimeters, and they are usually specified using a standard numbering system. The most common O-ring sizes are based on the American Society for Testing and Materials (ASTM) standard, which provides a range of sizes to suit different applications. When selecting an O-ring size, it's essential to ensure that it matches the specifications of your system, taking into account the ID, OD, and width of the groove. You should also consider the type of material and the operating conditions to ensure that the O-ring can withstand the stresses and pressures involved.O-Ring Material Selection
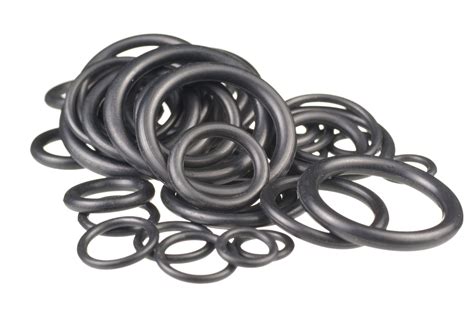
Factors Affecting O-Ring Performance
Several factors can affect the performance of an O-ring, including the operating temperature, system pressure, and type of fluid or gas being used. Extreme temperatures, for example, can cause O-rings to become brittle or soft, leading to premature wear and failure. Similarly, high system pressures can cause O-rings to become compressed or deformed, reducing their sealing effectiveness. The type of fluid or gas being used can also affect O-ring performance, as some materials may be incompatible with certain substances. By considering these factors and selecting the correct O-ring size and material, you can minimize the risk of O-ring failure and ensure reliable system performance.Measuring O-Ring Size
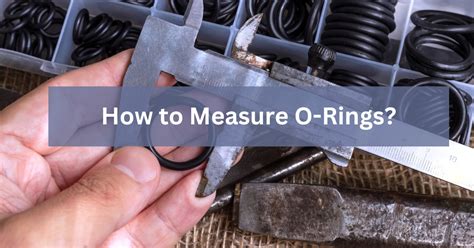
O-Ring Size Tolerances
O-ring size tolerances refer to the allowable variations in size that can affect the sealing effectiveness of the O-ring. The tolerance of an O-ring will depend on the type of material and the manufacturing process used. Generally, O-rings with tighter tolerances are more expensive to produce, but they offer superior sealing performance and reliability. When selecting an O-ring, it's essential to consider the tolerance of the O-ring, as well as the specifications of your system, to ensure that the O-ring can provide a reliable seal.O-Ring Installation Tips
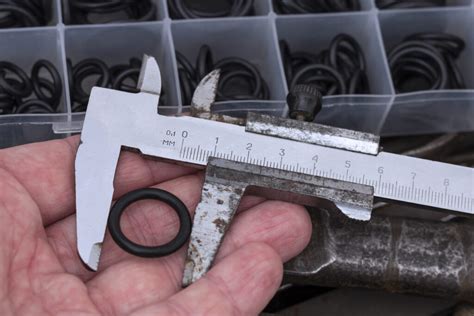
Common O-Ring Installation Mistakes
Several common mistakes can occur during O-ring installation, including over-tightening, under-tightening, and using the wrong installation tools. Over-tightening, for example, can cause the O-ring to become compressed or deformed, reducing its sealing effectiveness. Under-tightening, on the other hand, can allow the O-ring to move or shift during operation, leading to premature wear and failure. By avoiding these common mistakes, you can ensure that your O-ring is installed correctly and provides a reliable seal.O-Ring Maintenance and Replacement
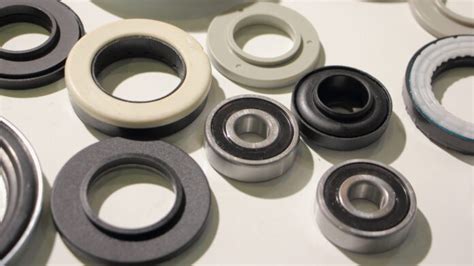
O-Ring Replacement Tips
Replacing an O-ring can be a challenging task, especially in complex systems or hard-to-reach areas. When replacing an O-ring, it's essential to follow a few simple tips, including using the correct replacement O-ring, following the manufacturer's instructions, and taking necessary safety precautions. You should also ensure that the new O-ring is properly seated in the groove, with no twists or kinks that can affect its sealing effectiveness. By following these tips, you can ensure that your O-ring is replaced correctly and provides a reliable seal.O-Ring Size Tips Image Gallery
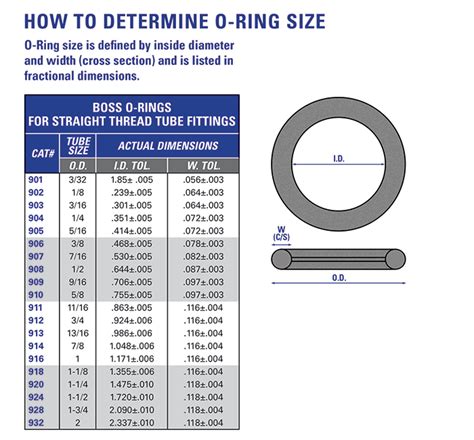
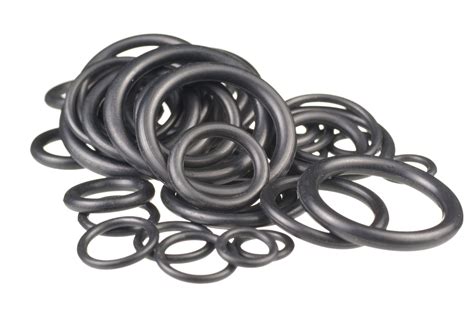
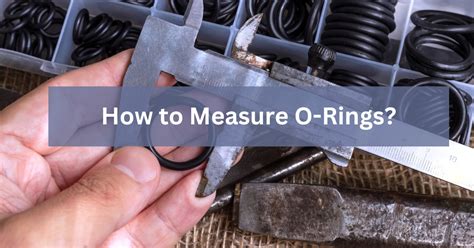
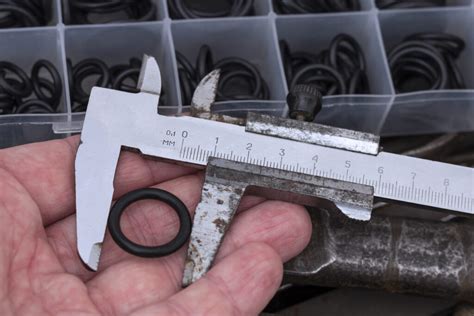
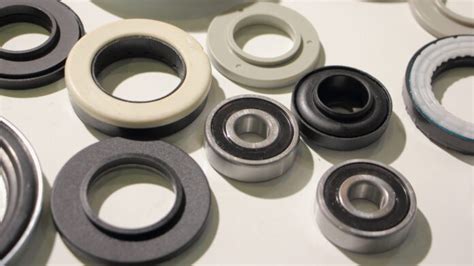
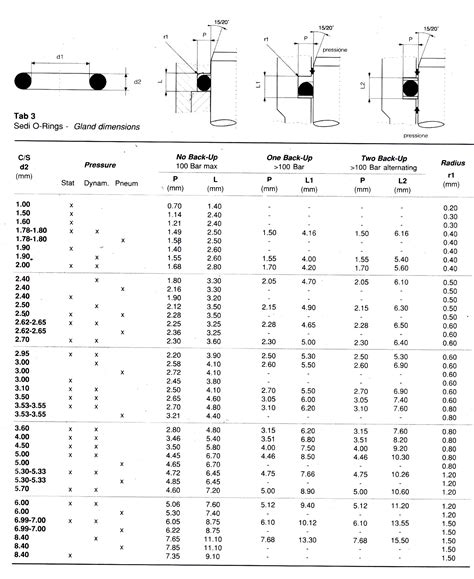
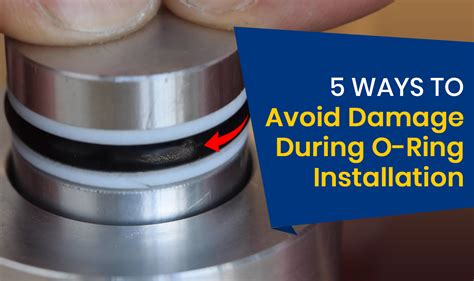
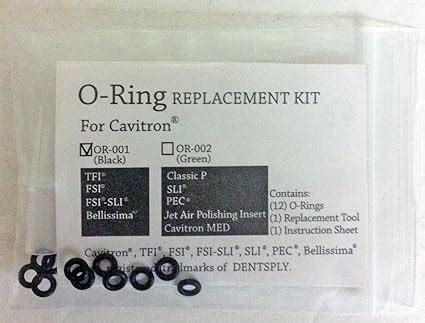
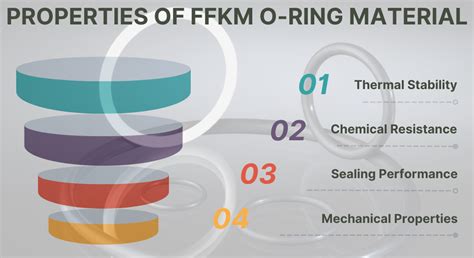
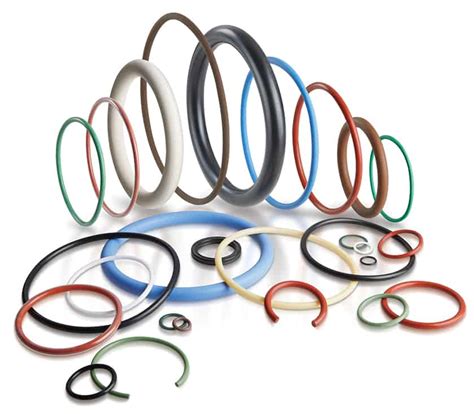
What is the importance of selecting the correct O-ring size?
+Selecting the correct O-ring size is crucial to ensure reliable system performance, prevent premature wear, and reduce the risk of equipment failure.
How do I measure O-ring size?
+To measure O-ring size, you need to determine the ID, OD, and width of the groove using tools such as calipers, micrometers, or measuring tapes.
What are the common mistakes to avoid during O-ring installation?
+Common mistakes to avoid during O-ring installation include over-tightening, under-tightening, and using the wrong installation tools.
How often should I replace my O-rings?
+O-rings should be replaced regularly, depending on the application and operating conditions. It's essential to follow a regular maintenance schedule and inspect your O-rings for signs of wear or damage.
What are the benefits of using the correct O-ring material?
+Using the correct O-ring material can provide superior sealing performance, resistance to temperature and pressure, and compatibility with various fluids and gases.
In conclusion, selecting the correct O-ring size is a critical step in ensuring reliable system performance and preventing premature wear. By following the tips and guidelines outlined in this article, you can ensure that your O-rings provide a reliable seal and minimize the risk of equipment failure. Remember to consider the ID, OD, and width of the groove, as well as the operating temperature, system pressure, and type of fluid or gas being used. With the right O-ring size and material, you can enjoy optimal system performance, reduced maintenance costs, and improved overall efficiency. We invite you to share your thoughts and experiences with O-ring sizing and selection in the comments below.