Intro
Discover expert 3D printable bearing tips for smooth motion, including lubrication, material selection, and design optimization for frictionless performance and durability in 3D printed mechanisms and robotics applications.
The world of 3D printing has revolutionized the way we create and innovate, allowing us to bring complex designs to life with ease. One of the most exciting applications of 3D printing is in the creation of custom bearings, which can be used in a wide range of industries, from robotics to aerospace. However, designing and printing 3D printable bearings can be a daunting task, especially for those who are new to the world of 3D printing. In this article, we will delve into the world of 3D printable bearings, exploring the benefits, challenges, and best practices for designing and printing these complex components.
The importance of bearings in mechanical systems cannot be overstated. Bearings are used to reduce friction and allow for smooth movement between two surfaces, making them a crucial component in everything from gears and motors to wheels and axles. Traditional bearings are often made from metal or ceramic materials, which can be heavy, expensive, and difficult to manufacture. 3D printed bearings, on the other hand, offer a number of advantages, including reduced weight, increased design flexibility, and lower production costs.
As we explore the world of 3D printable bearings, it's essential to understand the key considerations that go into designing and printing these complex components. From the type of material used to the printing technique employed, every aspect of the design and printing process can impact the performance and durability of the bearing. Whether you're a seasoned engineer or a hobbyist looking to create custom bearings for your next project, this article will provide you with the tips and insights you need to succeed.
Introduction to 3D Printable Bearings
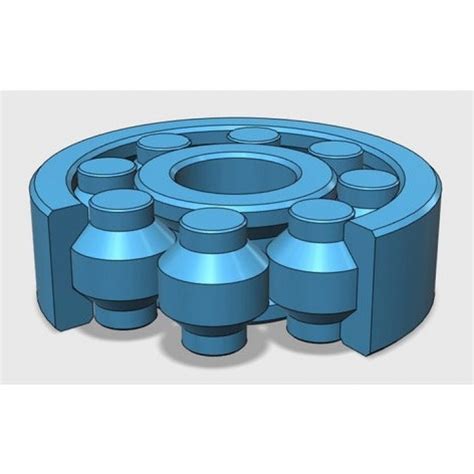
3D printable bearings are a type of bearing that is designed and manufactured using 3D printing technology. These bearings are typically made from plastic or metal materials and are designed to provide low friction and smooth movement between two surfaces. 3D printable bearings are often used in applications where traditional bearings are not feasible, such as in complex geometries or custom designs.
One of the key benefits of 3D printable bearings is their ability to be customized to meet specific design requirements. Unlike traditional bearings, which are often limited by their standard sizes and shapes, 3D printable bearings can be designed to fit precise specifications, making them ideal for use in complex mechanical systems. Additionally, 3D printable bearings can be made from a wide range of materials, including plastics, metals, and ceramics, allowing designers to choose the material that best suits their application.
Benefits of 3D Printable Bearings
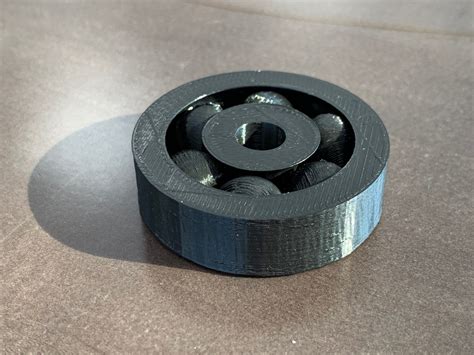
The benefits of 3D printable bearings are numerous and varied. Some of the key advantages of these bearings include:
- Reduced weight: 3D printed bearings are often made from lightweight materials, making them ideal for use in applications where weight is a concern.
- Increased design flexibility: 3D printable bearings can be designed to meet precise specifications, allowing designers to create complex geometries and custom shapes.
- Lower production costs: 3D printing technology allows for rapid prototyping and production, reducing the time and cost associated with traditional manufacturing methods.
- Improved performance: 3D printable bearings can be designed to provide optimal performance, with features such as customized lubrication channels and optimized surface finishes.
Challenges of 3D Printable Bearings
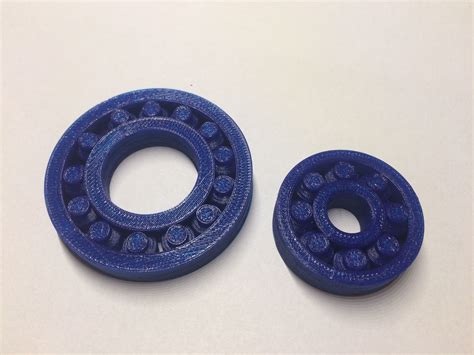
While 3D printable bearings offer a number of advantages, there are also several challenges associated with their design and manufacture. Some of the key challenges include:
- Material limitations: 3D printed bearings are often made from materials that have limited strength and durability, which can impact their performance and lifespan.
- Printing technique: The printing technique used to manufacture 3D printable bearings can impact their surface finish, accuracy, and overall quality.
- Assembly and integration: 3D printable bearings often require specialized assembly and integration techniques, which can add complexity and cost to the manufacturing process.
Design Considerations for 3D Printable Bearings
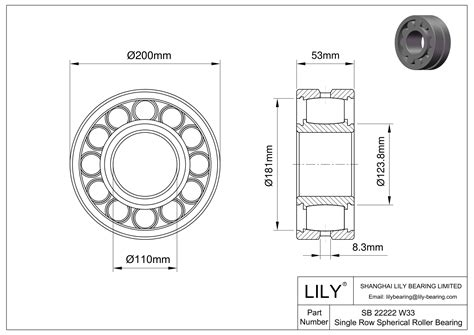
When designing 3D printable bearings, there are several key considerations that must be taken into account. Some of the most important design considerations include:
- Material selection: The material used to manufacture the bearing must be chosen based on its strength, durability, and compatibility with the application.
- Geometry and shape: The geometry and shape of the bearing must be designed to provide optimal performance, with features such as customized lubrication channels and optimized surface finishes.
- Tolerances and clearances: The tolerances and clearances of the bearing must be carefully controlled to ensure smooth movement and minimal friction.
- Assembly and integration: The design of the bearing must take into account the assembly and integration process, with features such as snap-fit components and guided assembly.
Printing Techniques for 3D Printable Bearings
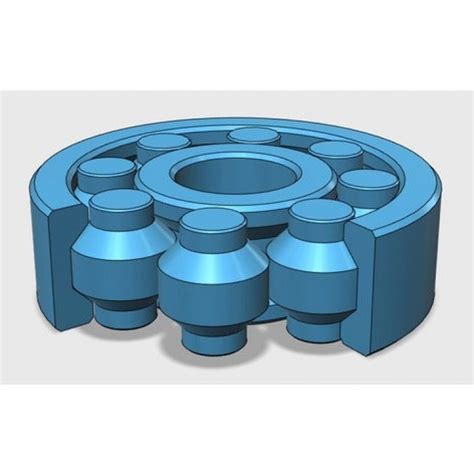
There are several printing techniques that can be used to manufacture 3D printable bearings, each with its own advantages and disadvantages. Some of the most common printing techniques include:
- Fused Deposition Modeling (FDM): FDM is a popular printing technique that uses melted plastic to create the bearing.
- Stereolithography (SLA): SLA is a printing technique that uses a laser to cure liquid resin, creating a highly accurate and detailed bearing.
- Selective Laser Sintering (SLS): SLS is a printing technique that uses a laser to fuse together powdered material, creating a strong and durable bearing.
Post-Processing Techniques for 3D Printable Bearings
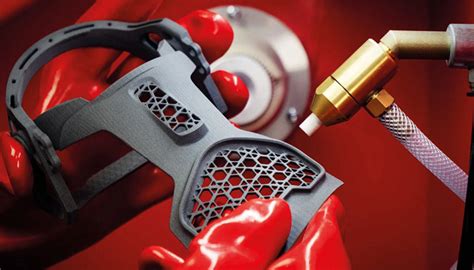
After printing, 3D printable bearings often require post-processing techniques to enhance their performance and durability. Some of the most common post-processing techniques include:
- Sanding and polishing: Sanding and polishing can be used to smooth out the surface finish of the bearing, reducing friction and improving performance.
- Heat treatment: Heat treatment can be used to enhance the strength and durability of the bearing, by relieving internal stresses and improving the material's microstructure.
- Coating and surface treatment: Coating and surface treatment can be used to enhance the bearing's corrosion resistance and wear resistance, by applying a thin layer of material to the surface.
Gallery of 3D Printable Bearings
3D Printable Bearings Image Gallery
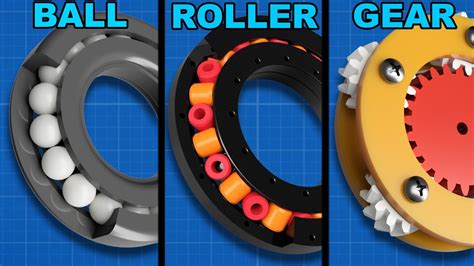
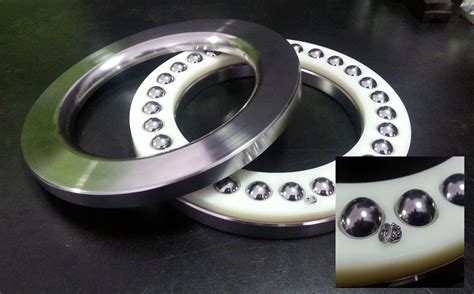
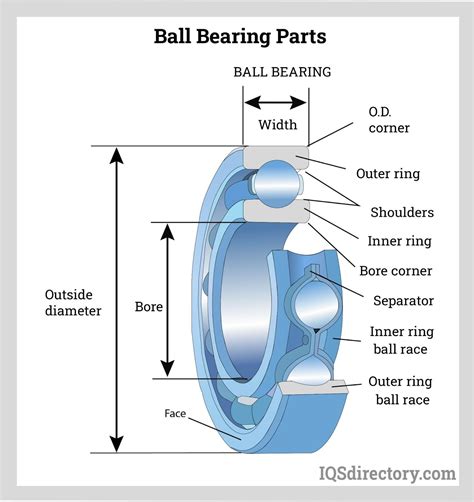
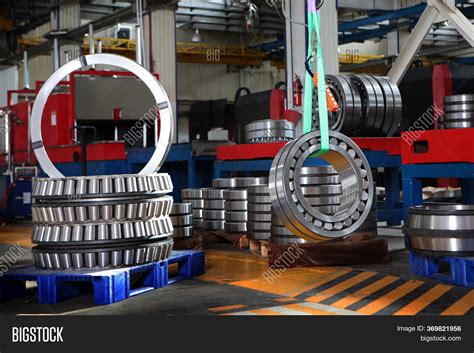
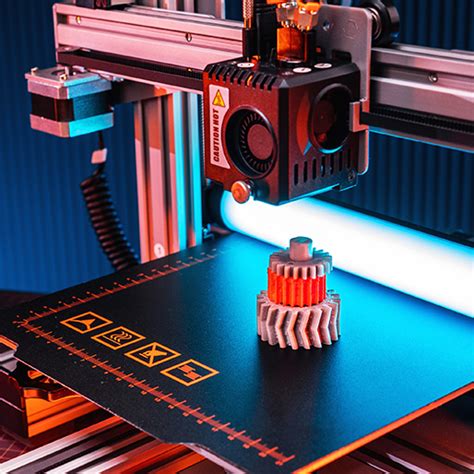
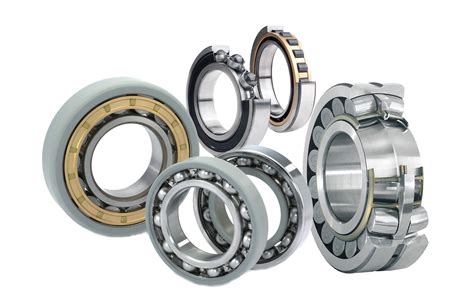
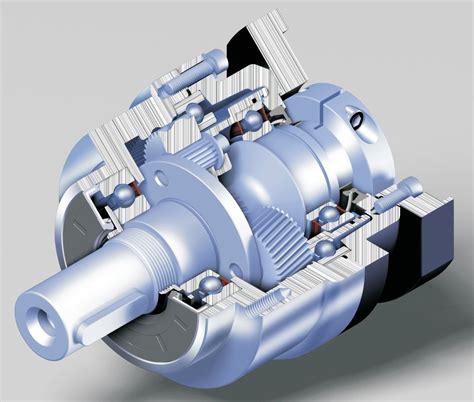
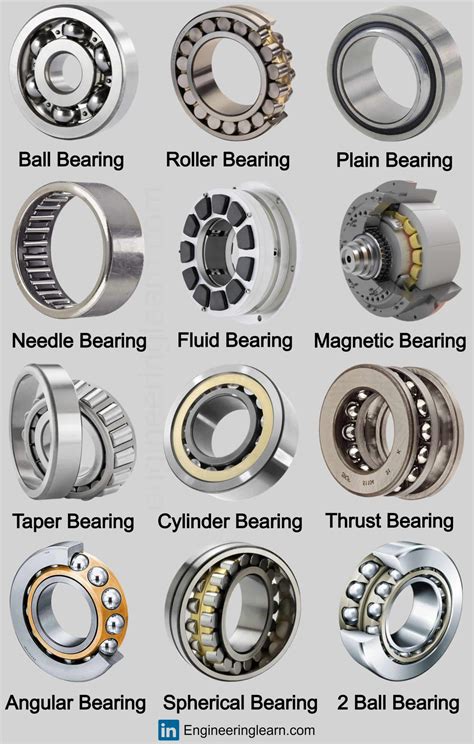
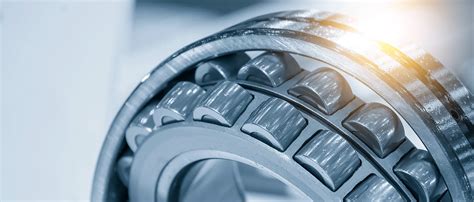
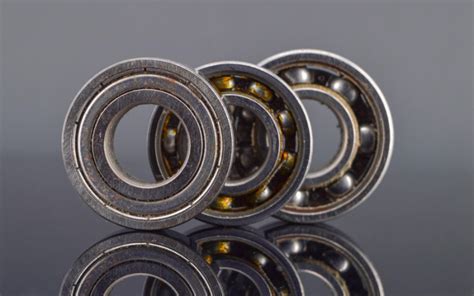
Frequently Asked Questions
What are 3D printable bearings?
+3D printable bearings are a type of bearing that is designed and manufactured using 3D printing technology.
What are the benefits of 3D printable bearings?
+The benefits of 3D printable bearings include reduced weight, increased design flexibility, and lower production costs.
What are the challenges of 3D printable bearings?
+The challenges of 3D printable bearings include material limitations, printing technique, and assembly and integration.
How are 3D printable bearings designed?
+3D printable bearings are designed using computer-aided design (CAD) software, taking into account factors such as material selection, geometry and shape, and tolerances and clearances.
What are the applications of 3D printable bearings?
+3D printable bearings have a wide range of applications, including robotics, aerospace, and industrial machinery.
In conclusion, 3D printable bearings offer a number of advantages over traditional bearings, including reduced weight, increased design flexibility, and lower production costs. However, there are also several challenges associated with their design and manufacture, including material limitations, printing technique, and assembly and integration. By understanding the benefits and challenges of 3D printable bearings, designers and engineers can create custom bearings that meet precise specifications and provide optimal performance. Whether you're a seasoned engineer or a hobbyist looking to create custom bearings for your next project, we hope this article has provided you with the tips and insights you need to succeed. We invite you to share your thoughts and experiences with 3D printable bearings in the comments below, and to explore the many resources available online for learning more about this exciting technology.