Intro
Discover innovative 3D printable spring designs, featuring flexible models, coil configurations, and tension-based prototypes, perfect for makers and engineers seeking customizable compression and torsion solutions.
The world of 3D printing has revolutionized the way we create and design objects, allowing for unprecedented levels of complexity and customization. One area where 3D printing has shown tremendous potential is in the creation of spring designs. Springs are essential components in a wide range of applications, from mechanical devices to furniture, and 3D printing has made it possible to create complex spring geometries that were previously impossible to produce using traditional manufacturing methods. In this article, we will explore the importance of 3D printable spring designs, their benefits, and the various types of springs that can be created using 3D printing technology.
The importance of springs cannot be overstated, as they play a critical role in many mechanical systems, providing the necessary force and flexibility to enable movement and functionality. However, traditional spring manufacturing methods often involve complex and time-consuming processes, such as coiling and machining, which can limit the design possibilities and increase production costs. 3D printing has changed this landscape, allowing designers and engineers to create complex spring geometries with ease, using a wide range of materials and printing technologies.
The benefits of 3D printable spring designs are numerous, including increased design flexibility, reduced production costs, and improved performance. By using 3D printing, designers can create springs with complex geometries, such as non-uniform coil pitches and variable diameters, which can improve the spring's mechanical properties and reduce the risk of failure. Additionally, 3D printing enables the creation of customized springs with specific properties, such as stiffness and damping, which can be tailored to meet the requirements of specific applications.
Introduction to 3D Printable Spring Designs
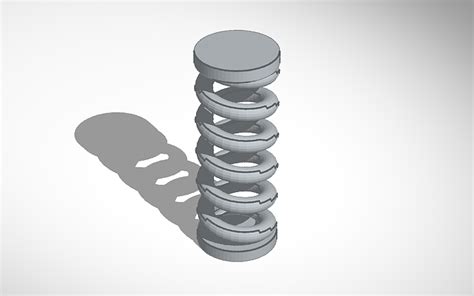
3D printable spring designs have opened up new possibilities for designers and engineers, allowing them to create complex and customized springs with ease. The use of 3D printing technology has enabled the creation of springs with unique geometries, such as helical and spiral springs, which can provide improved mechanical properties and reduced weight. Additionally, 3D printing has made it possible to create springs with integrated features, such as attachment points and sensors, which can simplify assembly and improve performance.
Types of 3D Printable Springs
There are several types of springs that can be created using 3D printing technology, including: * Helical springs: These are the most common type of spring and are characterized by a coil shape with a constant pitch and diameter. * Spiral springs: These springs have a coil shape with a variable pitch and diameter, which can provide improved mechanical properties and reduced weight. * Torsion springs: These springs are designed to store energy when twisted and are commonly used in applications such as door hinges and garage doors. * Compression springs: These springs are designed to store energy when compressed and are commonly used in applications such as shock absorbers and engine mounts.Benefits of 3D Printable Spring Designs
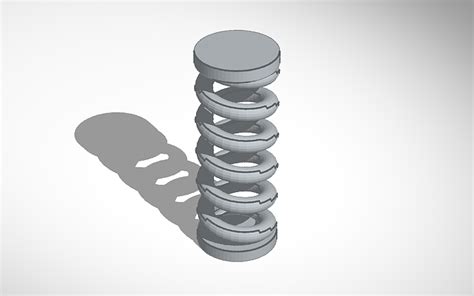
The benefits of 3D printable spring designs are numerous and include:
- Increased design flexibility: 3D printing enables the creation of complex spring geometries, such as non-uniform coil pitches and variable diameters, which can improve the spring's mechanical properties and reduce the risk of failure.
- Reduced production costs: 3D printing can reduce production costs by eliminating the need for tooling and minimizing material waste.
- Improved performance: 3D printing enables the creation of customized springs with specific properties, such as stiffness and damping, which can be tailored to meet the requirements of specific applications.
Materials Used for 3D Printable Spring Designs
The materials used for 3D printable spring designs are diverse and include: * Metals: Such as aluminum, steel, and titanium, which are commonly used for high-strength and high-temperature applications. * Polymers: Such as ABS, PLA, and nylon, which are commonly used for low-cost and low-weight applications. * Composites: Such as carbon fiber and glass fiber, which are commonly used for high-performance and high-strength applications.Applications of 3D Printable Spring Designs
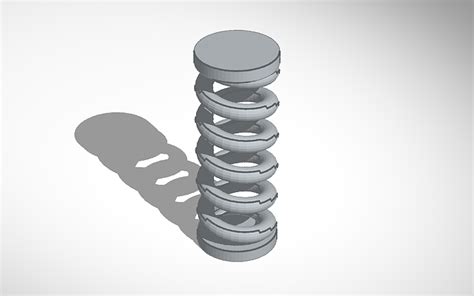
The applications of 3D printable spring designs are numerous and include:
- Aerospace: 3D printed springs are used in aircraft and spacecraft to reduce weight and improve performance.
- Automotive: 3D printed springs are used in vehicles to improve suspension and reduce vibration.
- Medical: 3D printed springs are used in medical devices, such as implants and prosthetics, to improve performance and reduce risk of failure.
- Consumer products: 3D printed springs are used in consumer products, such as furniture and appliances, to improve performance and reduce cost.
Design Considerations for 3D Printable Spring Designs
When designing 3D printable spring designs, there are several considerations to keep in mind, including: * Material selection: The material selected should be suitable for the application and should have the necessary mechanical properties. * Geometry: The geometry of the spring should be designed to provide the necessary mechanical properties and to minimize the risk of failure. * Printing technology: The printing technology used should be suitable for the material and geometry selected.Challenges and Limitations of 3D Printable Spring Designs
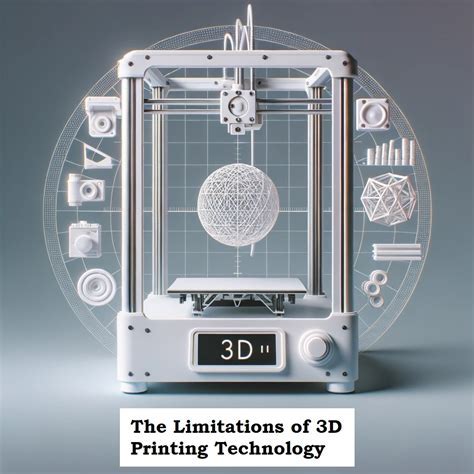
Despite the numerous benefits of 3D printable spring designs, there are several challenges and limitations to consider, including:
- Material limitations: The materials used for 3D printing may have limited mechanical properties, such as strength and stiffness.
- Printing technology limitations: The printing technology used may have limitations, such as resolution and accuracy.
- Cost: 3D printing can be expensive, especially for complex geometries and high-performance materials.
Future Developments in 3D Printable Spring Designs
The future of 3D printable spring designs is promising, with several developments on the horizon, including: * Improved printing technologies: New printing technologies, such as 4D printing, are being developed to improve the resolution and accuracy of 3D printed springs. * New materials: New materials, such as advanced composites and smart materials, are being developed to improve the mechanical properties and performance of 3D printed springs. * Increased adoption: 3D printing is becoming increasingly adopted in various industries, including aerospace, automotive, and medical, which is driving the development of new 3D printable spring designs.3D Printable Spring Designs Image Gallery
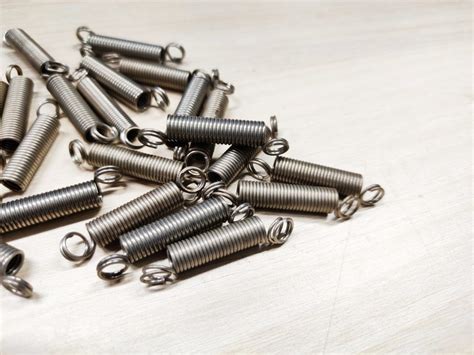
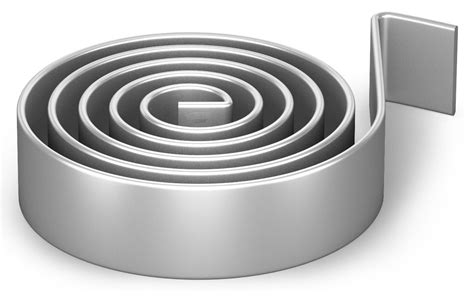
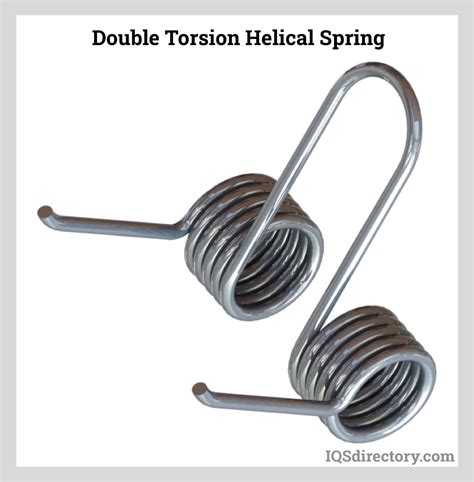
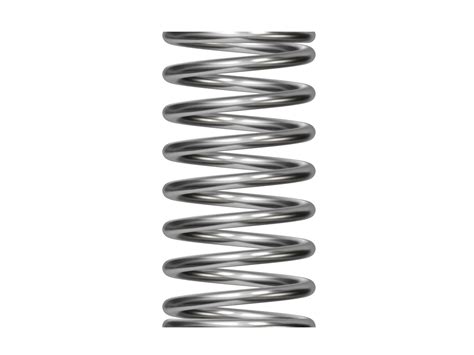
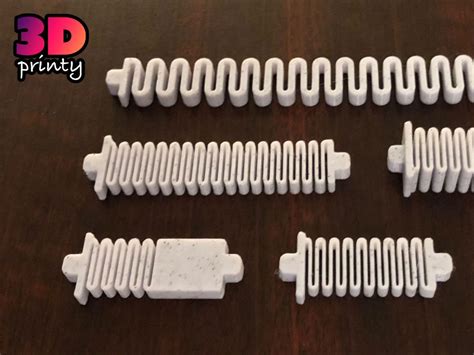
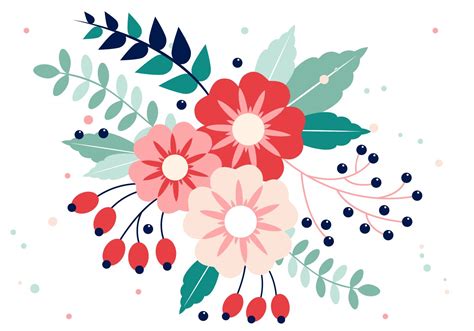
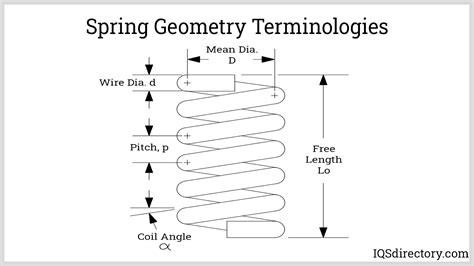
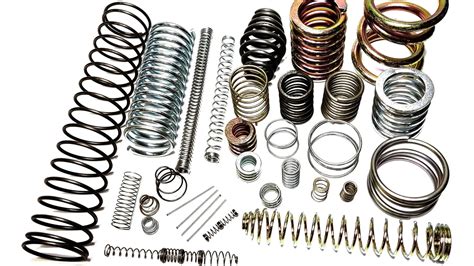
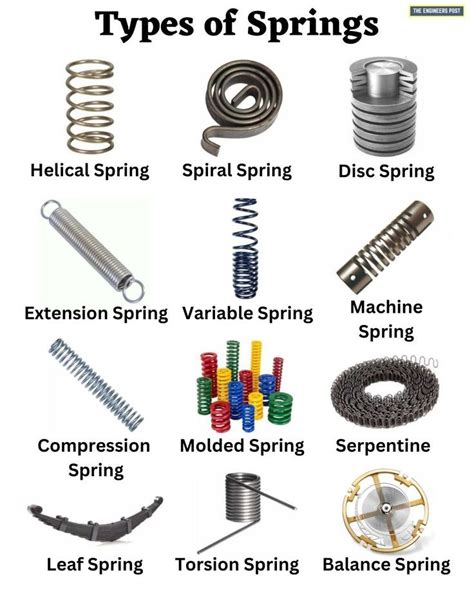
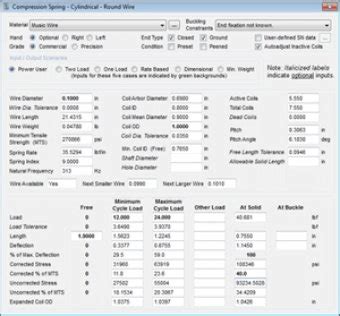
What are the benefits of 3D printable spring designs?
+The benefits of 3D printable spring designs include increased design flexibility, reduced production costs, and improved performance.
What types of springs can be created using 3D printing technology?
+Several types of springs can be created using 3D printing technology, including helical springs, spiral springs, torsion springs, and compression springs.
What materials can be used for 3D printable spring designs?
+The materials used for 3D printable spring designs are diverse and include metals, polymers, and composites.
In summary, 3D printable spring designs have revolutionized the way we create and design springs, offering increased design flexibility, reduced production costs, and improved performance. With the ability to create complex geometries and customized springs, 3D printing has opened up new possibilities for designers and engineers. As the technology continues to evolve, we can expect to see even more innovative and complex spring designs in the future. We invite you to share your thoughts and experiences with 3D printable spring designs in the comments below, and to explore the many resources available online for learning more about this exciting technology.