Intro
Discover 3D printable gears, including customizable designs, gear templates, and mechanical components, to enhance your 3D printing projects with precise gear systems and mechanisms.
The world of 3D printing has revolutionized the way we design and manufacture objects, and one of the most fascinating applications of this technology is the creation of 3D printable gears. Gears are an essential component in many mechanical systems, and being able to print them on demand can greatly simplify the design and prototyping process. In this article, we will delve into the world of 3D printable gears, exploring their benefits, working mechanisms, and the steps involved in creating them.
The importance of gears in mechanical systems cannot be overstated. They are used to transmit power, change the speed or direction of rotation, and adjust the torque of a system. With the advent of 3D printing, designers and engineers can now create custom gears with complex geometries and precise tolerances, which can be used in a wide range of applications, from robotics and automotive systems to medical devices and consumer products. The ability to print gears on demand also reduces the need for inventory storage and minimizes the lead time for production, making it an attractive option for companies looking to streamline their manufacturing processes.
The benefits of 3D printable gears are numerous. For one, they can be designed with complex geometries that would be difficult or impossible to produce using traditional manufacturing methods. This allows designers to create gears with optimized performance characteristics, such as reduced weight, increased strength, and improved efficiency. Additionally, 3D printed gears can be produced with a high degree of precision, which is critical in applications where gear failure can have serious consequences. The use of 3D printing also enables the rapid prototyping of gear designs, allowing designers to test and refine their creations quickly and efficiently.
Introduction to 3D Printable Gears
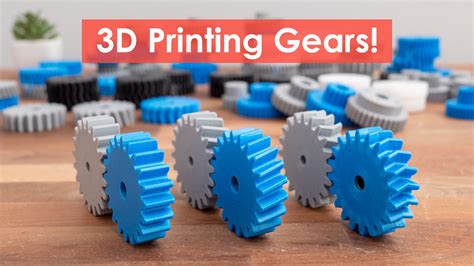
To create 3D printable gears, designers use computer-aided design (CAD) software to create a digital model of the gear. The CAD model is then sliced into thin layers, which are used to generate the printing instructions for the 3D printer. The 3D printer reads the instructions and lays down the layers of material, such as plastic or metal, to create the gear. The printing process can take anywhere from a few minutes to several hours, depending on the complexity of the gear design and the capabilities of the 3D printer.
Benefits of 3D Printable Gears
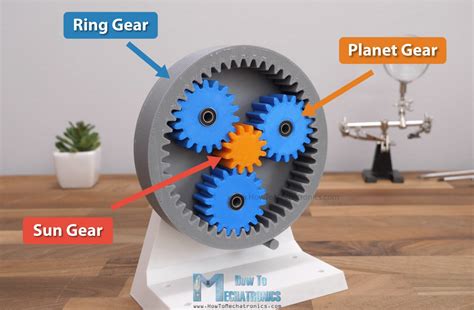
Some of the key benefits of 3D printable gears include:
- Rapid prototyping and production
- Complex geometries and customized designs
- High precision and accuracy
- Reduced material waste and energy consumption
- Increased design flexibility and freedom
Working Mechanisms of 3D Printable Gears
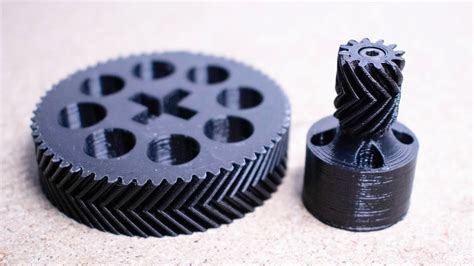
The working mechanisms of 3D printable gears are similar to those of traditionally manufactured gears. They are designed to transmit power, change the speed or direction of rotation, and adjust the torque of a system. However, 3D printed gears can be designed with unique features and characteristics that take advantage of the capabilities of 3D printing. For example, 3D printed gears can be designed with internal structures and geometries that cannot be produced using traditional manufacturing methods.
Steps Involved in Creating 3D Printable Gears
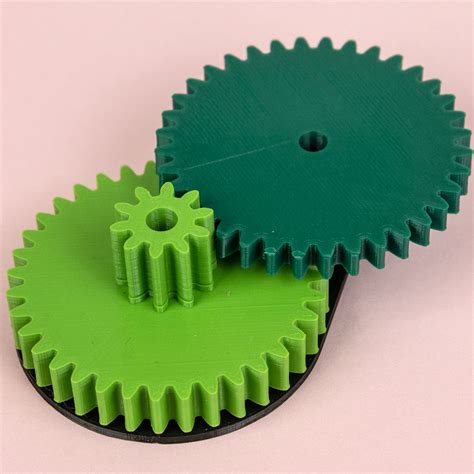
The steps involved in creating 3D printable gears include:
- Designing the gear using CAD software
- Slicing the CAD model into thin layers
- Generating the printing instructions for the 3D printer
- Printing the gear using the 3D printer
- Post-processing the gear to remove any support material and achieve the desired finish
Applications of 3D Printable Gears
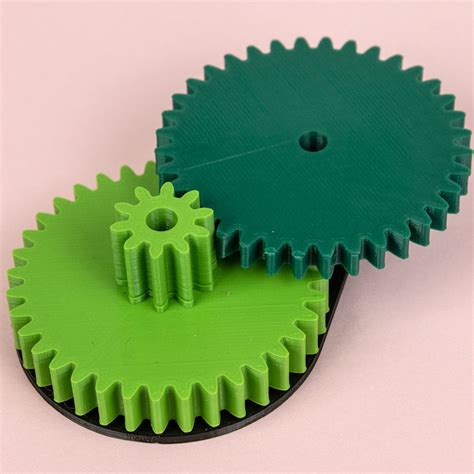
The applications of 3D printable gears are diverse and widespread. They can be used in a wide range of industries, including:
- Robotics and automation
- Automotive and aerospace
- Medical devices and healthcare
- Consumer products and appliances
- Industrial machinery and equipment
Challenges and Limitations of 3D Printable Gears
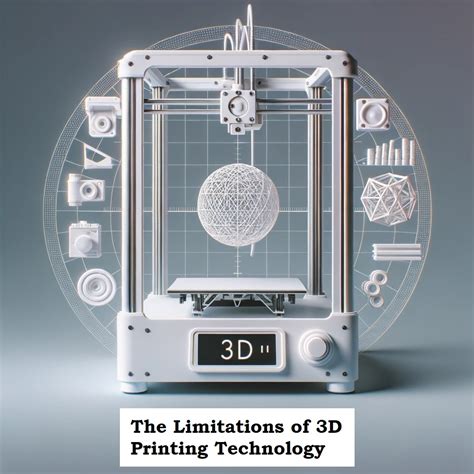
While 3D printable gears offer many benefits and advantages, there are also some challenges and limitations to consider. These include:
- Material limitations and properties
- Printing resolution and accuracy
- Post-processing and finishing requirements
- Cost and accessibility of 3D printing technology
Future Developments and Trends in 3D Printable Gears
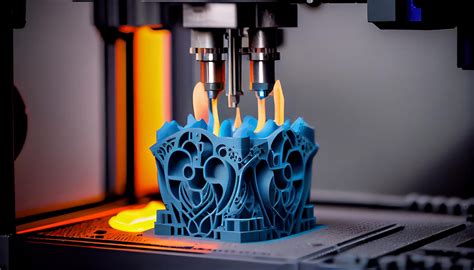
The future of 3D printable gears is exciting and promising. As 3D printing technology continues to evolve and improve, we can expect to see:
- Advances in material properties and performance
- Improvements in printing resolution and accuracy
- Increased accessibility and affordability of 3D printing technology
- New and innovative applications of 3D printable gears
Gallery of 3D Printable Gears
3D Printable Gears Image Gallery
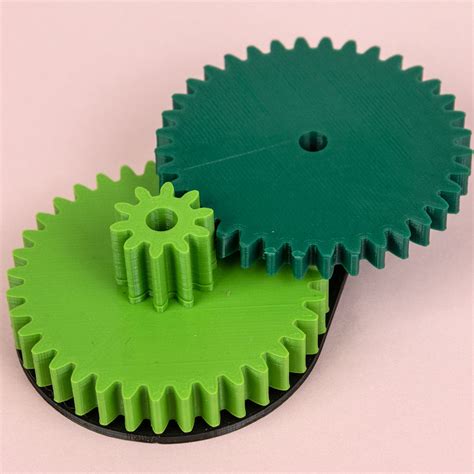
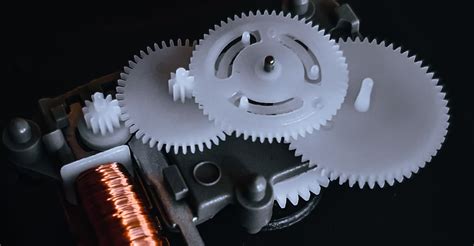
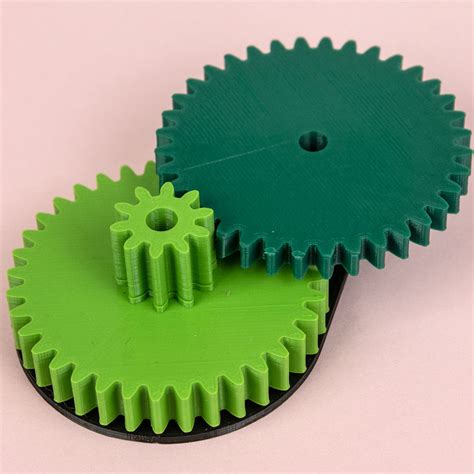
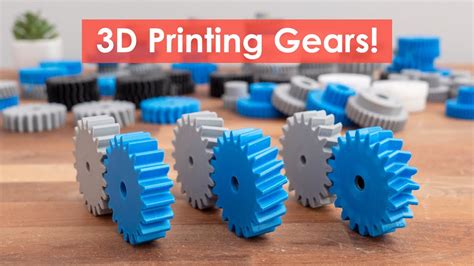
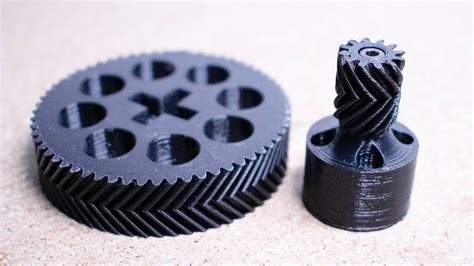
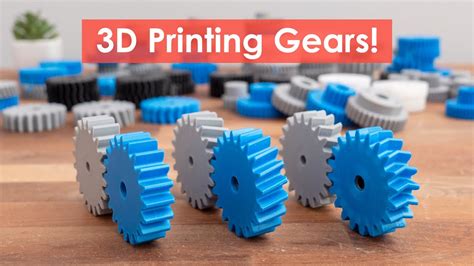
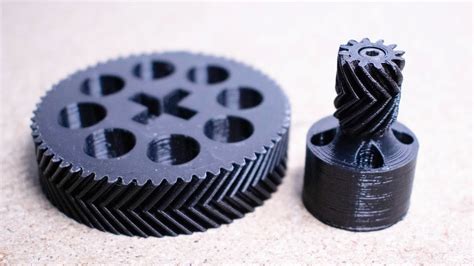
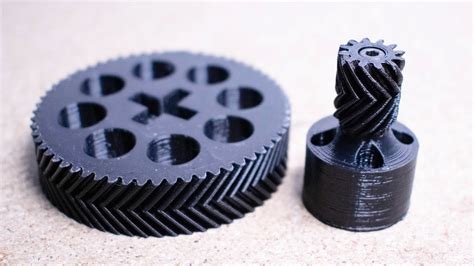
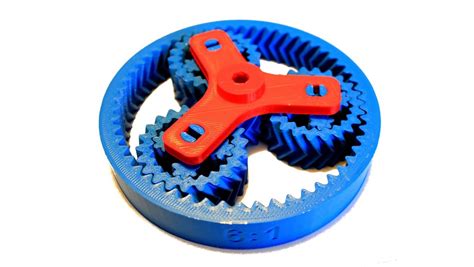
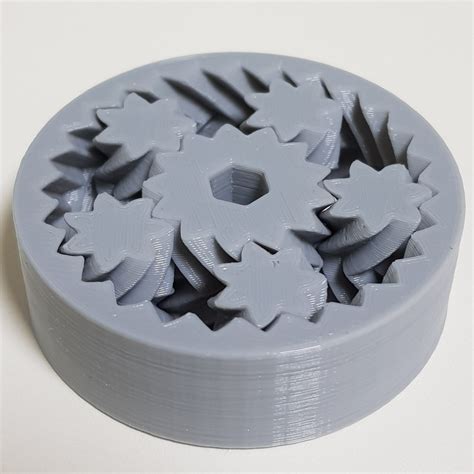
What are the benefits of using 3D printable gears?
+The benefits of using 3D printable gears include rapid prototyping and production, complex geometries and customized designs, high precision and accuracy, reduced material waste and energy consumption, and increased design flexibility and freedom.
What are the challenges and limitations of 3D printable gears?
+The challenges and limitations of 3D printable gears include material limitations and properties, printing resolution and accuracy, post-processing and finishing requirements, and cost and accessibility of 3D printing technology.
What are the future developments and trends in 3D printable gears?
+The future developments and trends in 3D printable gears include advances in material properties and performance, improvements in printing resolution and accuracy, increased accessibility and affordability of 3D printing technology, and new and innovative applications of 3D printable gears.
In conclusion, 3D printable gears are a rapidly evolving field that offers many benefits and advantages over traditional manufacturing methods. With the ability to create complex geometries and customized designs, 3D printed gears can be used in a wide range of applications, from robotics and automotive systems to medical devices and consumer products. As 3D printing technology continues to improve and advance, we can expect to see even more innovative and exciting developments in the field of 3D printable gears. We invite you to share your thoughts and experiences with 3D printable gears, and to explore the many resources and tutorials available online to learn more about this fascinating topic. Whether you are a seasoned engineer or a hobbyist, 3D printable gears are an exciting and rapidly evolving field that is sure to capture your imagination and inspire your creativity.